Electric Servo End Forming Machine (1003 EL) for the Tube Forming Industry
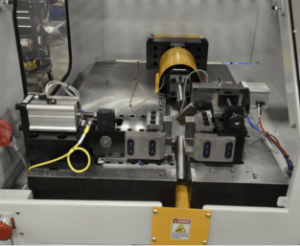
Case Study
Dedicated to providing our clients with the highest quality tool development and machine building products and services, Wauseon Machine manufactures the model 1003 end forming machine, displayed on the left. The end forming machines are available in both hydraulic and electric construction. However, electric end forming machinery offers more efficiency and less waste than its hydraulic counterpart, making this version more environmentally friendly.
In addition, all electrical models possess the following features:
- Multi-language graphical user interface (GUI)
- Low pressure lock-up
- Automatic drop-out
- Quick change tooling
To better ensure product quality, we thoroughly inspect all machinery before any finished item is delivered to our customer. Wauseon Machine verifies the end forming machine’s center line by grinding wear plates in lock-up area, and runs a 20-hour dry cycle prior to shipping. Moreover, all manufactured components of the machine come with inspection reports prior to assembly. These comprehensive inspections guarantee that our clients receive the quality they have long come to expect from our products.
All of our 1003 EL end forming machines can be built to Charlie Edwards (CE) and Ontario Hydro certifications. Special voltages are also available with both hydraulic and electric models.
Wauseon Machine’s standard line of end forming equipment, including the model 1003 EL, offers the smallest footprint in the industry
1003 Electric Servo end Forming Machine for the Tube Fabricating Industry Specifications
Capabilities Applied/Processes | Engineering Design Electrical Programming Welding Assembly |
Overall Machine Dimensions | Width: 41 ¼” Depth: 66″ |
Tubing Diameter | Can form up to 5/8″ diameter .049″ wall steel tube ends |
Material Used | Precision ground steel slides |
Material Finish | Painting done in-house Color: Wauseon Machine blue |
Standard Features | All electric servo driven (hydraulic also available) Multi-language graphical user interface (GUI) Low pressure lock-up Automatic drop-out Smallest foot print in industry Quick change tooling |
Specifications | Ram Force: 7 Tons # Of Strokes: 3 Tube Clamp Force: 9 Tons Ram Cylinder Bore: Servo Electromechanical Ram Stroke: 4.5″ Max. Clamp Opening: 1.5″ Cycle Rate: 1.7s to 4.3s Air Required: 80 psi, 2cfm Electrical Requirements: 230/460 VAC 3 Phase 60 hz FLA 50 Weight: 1960 lbs |
Available Options | Auto load/unload system Multi-language graphical user interface (GUI) Process lube system Custom specified paint colors Special voltages available |
Benefits of Electrical Design over Hydraulic | More Efficient Less Waste Greener Environment 31.11% faster machine cycle time* 16.23% faster total cycle time (including load and unload)* 377.5 fewer hours to produce 1 million parts* 155,993 more parts/year per shift* *Evaluation based on 260 days production with one 7.2 hour shift at 80% efficiency |
In process testing/inspection performed | All manufactured components include inspection reports prior to assembly Wauseon Machine verifies center line by grinding wear plates in lock up area 20 hour dry cycle is run prior to shipping to customer |
Industry for Use | Automotive, HVAC, Plumbing, Appliance, Aerospace, Hydraulic, Construction and Furniture |
Standards Met | Can be built to Charlie Edwards (CE) and Ontario Hydro Certifications. |
Product Name | 1003 EL End Forming Machine |