3D Printed Prototype of Reverse Engineered Part for the Foam Molding Industry
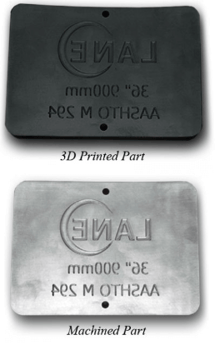
Case Study
A manufacturer of structural foam molding required design changes to a machined part, but they did not have the internal capability to quickly and cost effectively complete the job themselves.
The machined part was a plate insert that featured their customer’s company logo, which had recently been updated. In order to avoid hindering production, changes to the logo on the plate insert were urgent; however, a CAD model was not yet available for the new logo.
As a turn-key solution provider, Wauseon Machine was able to offer engineering services to design a CAD model of the new logo. Prior to manufacturing the part, a prototype sample was produced as part of our approval process for the logo design. To provide an economical prototype of the part, our engineering group inserted the new logo into a reverse-engineered CAD model of the plate insert and transferred the file to our in-house 3D printer. Within 10 hours, a sample part was available for delivery.
Upon receipt of the 3D printed prototype part, our customer requested some slight adjustments to the new logo. Our engineering team quickly revised the part print and released it to our CNC Toolroom for production. Thanks to the quick turn around time of our engineering department, our 3D printing capabilities, the dedication of our skilled Toolmakers, and the project management provided by the Account Manager, the expedited due date was achieved.
For more information on our reverse engineering capabilities or our 3D printing services, please contact us by email (sales@wauseonmachine.com)
or phone (419-337-0940)!